Tools & Resources
Steel Helps Strike The Right Solution For New bowling Centre
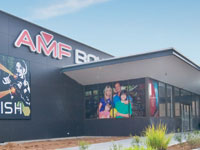
AMF Bowling & M9 Laser Skirmish, a complete design and construction package provided by BlueScope Buildings Australia.
Location: | Rooty Hill, Sydney, New South Wales |
Country: | Australia |
Architect: | Altis Architecture |
Builder: | Kell & Rigby |
Download: | Download Case Study: Steel Helps Strike The Right Solution For New Bowling Centre (693 KB) |
A unique design and construction package covering key elements of one of Sydney's newest leisure facilities has highlighted the winning formula adopted by BlueScope Buildings Australia.
The new AMF Bowling and M9 Laser Skirmish Rooty Hill RSL, in Sydney's west, will provide a popular new recreation venue for local residents and Club members.
Its creation underscored the sustainability of steel building technology, delivering significant cost savings stemming from the efficiency of the engineered structure together with labour and transport savings achieved during the building phase.
Builder Kell & Rigby, which is celebrating a century in business in 2010, won the tender to erect a design by Altis Architecture, based on a brief from the Club and AMF Bowling.
"The structural elements had already been designed when Kell & Rigby asked us to become involved," said BlueScope Buildings Australia Project Manager, Matt Simonis.
"We were able to provide a better structural solution, which we designed, fabricated and erected, as well as a roof cladding solution with the efficiency advantage of on-site roll forming and the premium LYSAGHT KLIP-LOK® concealed-fix roofing profile.
"Combining those two elements optimised the advantages of state-of-the-art steel building technology, with benefits during the building program and throughout the life of the building."
A key reason for the success of the BlueScope Buildings Australia package stemmed from cost savings that flowed from a design innovation, which used less steel than originally envisaged.
Paul Dickman, who headed the design team from Altis Architecture, recalled the reaction to the solution suggested by BlueScope Buildings Australia.
"Everyone was wowed by their clear space solution with its absence of columns – a completely column-free area with space for 34 bowling lanes – the largest continuous-lane bowling centre in Australia," he said.
"BlueScope used the experience of their American subsidiary to create tapered beams that gave clearspan areas up to 29-metres, with a single row of internal columns instead of the three envisaged in the original design."
"The design and construction package for the structure and the roof cladding happened very quickly," Paul Dickman said. "BlueScope Buildings were brought into the project in November 2009 and the first steel began to go up on site on December 18."
"The first bay was up before Christmas 2009, and within a week and a half after New Year the full structure was up and they were starting to roll roof on the main frame."
To achieve that progress BlueScope Buildings used a combination of design methodologies, fabrication techniques and supply chain management.
It supervised the construction of tapered beams that were cut from plate and fabricated on pull-through welding machines using a technique only a handful of companies in Australia have mastered.
It also provided engineering certification for the bowling and laser skirmish centre structure that benefits from extensive BlueScope Buildings' experience in China and the United States.
As part of its contribution to the success of the project, BlueScope Buildings organised for the steel framing to be stood, purlins and girts installed and the roof cladding to be rolled and fixed in a seamless succession of trades that at some stages saw roofing bays being erected while the previous one was clad.
"Because the steel went up so quickly we were tracking three weeks ahead, which is very impressive on a 26- week build," Paul Dickman said. "The onsite roll forming of the roof cladding was also very impressive and fast."
Rolled in continuous lengths up to 26-metres, the ZINCALUME® steel roofing solution minimises joints over the venue's 3,800 square metre area.
The design and construct package for the structure and roof cladding package makes sense," Paul Dickman said. "If BlueScope Buildings had been involved during the initial design phase the benefits for the build would have been even better."
"They indicated that with more time, different manufacturing options could have saved a further $50,000."
"Even though the whole process was very quick, we have already identified ways in which we can expedite the process and reduce project costs even more," BlueScope Buildings Project Manager Matt Simonis said.
"From a sustainability point of view our solution offered several advantages. The structure we engineered required significantly less steel than a conventional design and delivered cost savings for labour and materials.
"On-site roll forming with long-length sheets output direct to the roof also saved time, material handling and costs."
Steve Torta, Senior Project Manager for Kell & Rigby said the way the project came together obviously had benefits for the client.
"The one-stop-shop approach to the design, fabrication and erection produced a great result," he said. "It was new territory for us, so there were a few unknowns, but there is no questioning the outcome.
"I can see that the benefits would only increase on larger sites and larger projects."